Subsea Hydrostatic Testing
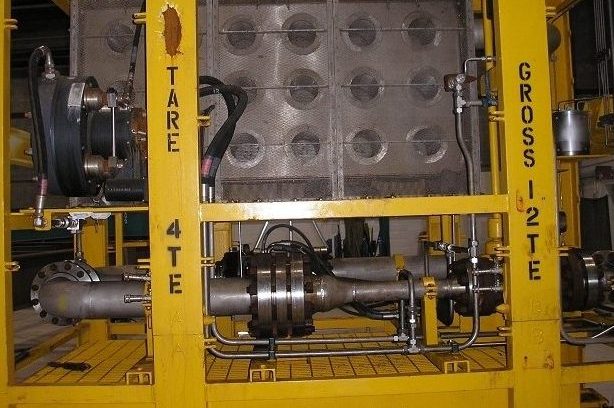
What is Subsea Hydrostatic Testing?
Subsea hydrostatic testing is a vital procedure used to ensure the strength and reliability of submerged pipes. In this process, high-pressure water is pumped into these pipes to assess their structural integrity. However, conducting such tests can be challenging and time-consuming, especially when it involves dropping long hoses from a support vessel into the depths of the sea.
Fortunately, technological advancements have brought about innovative solutions to simplify this process. One such solution is the remarkable Harben® pump, which offers a subsea version specifically designed for these demanding applications. This subsea version of the Harben® pump can be conveniently mounted onto any skid, making it incredibly versatile and adaptable to various testing scenarios.
One of the key advantages of the subsea Harben® pump is its ease of pressure compensation. This means that it can readily adjust to the underwater conditions and maintain the desired pressure levels consistently throughout the testing process. Additionally, the pump is specifically engineered to be sea water tolerant, which is crucial considering its subsea application. This feature ensures that the pump can withstand the corrosive effects of saltwater, enhancing its durability and overall performance.
By utilizing the subsea Harben® pump, the process of subsea hydrostatic testing becomes more efficient, reliable, and safer. The ability to mount the pump on a skid on the seabed eliminates the need for long hose drops from a support vessel, simplifying the setup and reducing potential risks associated with hose deployment.
In conclusion, the subsea Harben® pump offers an excellent solution for subsea hydrostatic testing. Its adaptability, ease of pressure compensation, and sea water tolerance make it a reliable and efficient tool in ensuring the structural integrity of submerged pipes. Embracing such innovative technologies brings us closer to conducting subsea operations with enhanced precision and safety.
Subsea High Pressure Pumps
The Harben® pump stands strong even in the face of challenging conditions, such as operating at depths of several hundred meters for extended periods. Its remarkable reliability remains intact, thanks to its ingenious design. One key element contributing to its endurance is the implementation of high-pressure rubber diaphragms. These diaphragms act as barriers, separating the working components of the pump from the media being pumped. As a result, wear rates are significantly reduced, and the occurrence of downtime is minimized, ensuring consistent performance even in demanding environments.
When it comes to hydrostatic pressure testing, the Harben® pump excels with its impressive capabilities. It boasts a remarkable working pressure capacity of up to 700 bar, allowing it to handle high-pressure testing requirements with ease. Additionally, its maximum flow rate of 135 liters per minute ensures efficient and speedy operations. This makes the pump an ideal choice for various hydrostatic pressure testing applications, where precise and accurate results are essential.
What sets the Harben® pump apart is its multi-cylinder design, which offers remarkable flexibility and control. This design enables turn-down ratios of up to 10:1, allowing for the adjustment of flow rates while maintaining a smooth and consistent output flow. Such fine-tuned control is invaluable in situations where accuracy and precision are paramount.
The Harben® pump’s resilience and unwavering reliability make it a trusted companion in the most challenging environments. Its high-pressure rubber diaphragms and efficient design reduce wear rates and downtime, ensuring consistent performance. Whether it’s hydrostatic pressure testing or other demanding applications, the Harben® pump’s exceptional capabilities and precise control make it a go-to solution for professionals who prioritise efficiency and accuracy in their operations.
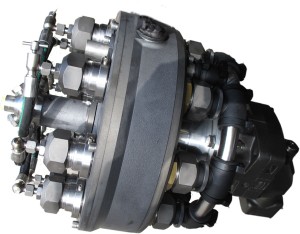